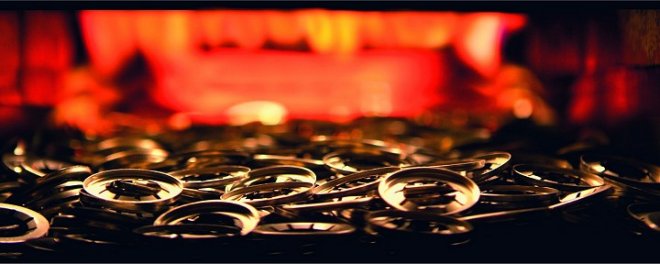
attas.it
IMPIANTI, ATTREZZATURE E PRODOTTI PER I TRATTAMENTI TERMICI
Il tuo partner ideale per i trattamenti termici
Dal 1979, siamo il punto di riferimento per aziende di ogni dimensione che cercano soluzioni innovative e affidabili nei trattamenti termici. Con oltre 40 anni di esperienza, offriamo una gamma completa di attrezzature, impianti e prodotti ausiliari, selezionati tra i migliori produttori a livello mondiale.
Perché scegliere ATTAS?
Esperienza
Un team di esperti al tuo servizio per trovare la soluzione più adatta alle tue esigenze.
Qualità
Prodotti e servizi certificati per garantire la massima affidabilità.
Personalizzazione
Soluzioni su misura per ottimizzare i tuoi processi e aumentare la produttività
Dalla sezione notizie
IL MEGLIO DELLA NITRURAZIONE!
RÜBIG GmbH
Il Vostro Partner ideale per la tecnologia delle superfici!
La tecnologia MICROPULS® PLASMA della RÜBIG® è la più avanzata nel campo dei trattamenti di nitrurazione ionica. I nostri Partner in tutto il mondo si affidano alla nostra esperienza maturata in oltre 20 anni di ricerca e sviluppo nel campo dei trattamenti termici e delle superfici per diversi settori, sia per sale tempra conto terzi che per produttori con propri reparti di trattamento termico.
RÜBIG® è leader anche nella progettazione e costruzione di impianti per la nitrurazione gassosa con soluzioni personalizzate per ogni esigenza. I nostri impianti della serie GASCON K2 sono sinonimo di efficienza e tecnologia avanzata nelcontrollo dei processi.
La tecnologia MICROPULS® PLASMA
La tecnologia MICROPULS® by RÜBIG® rappresenta lo stato dell'arte per gli impianti di nitrurazione ionica, di rivestimento con strati duri e DLC utilizzando la tecnologia brevettata dei generatori MICROPULS® PLASMA.
MICROPULS®
Everest
Impianti di nitrurazione ionica
Gli impianti MICROPULS® EVEREST by RÜBIG® mettono a disposizione dei nostri Clienti il meglio della tecnologia per la nitrurazione.
MICROPULS®
Procoat
impianti per rivestimenti
Gli impianti per rivestimenti by RÜBIG® consentono di ottenere rivestimenti con strati duri per stampi e utensili di altissima gamma.
MICROPULS®
DIAMOND Xtended
impianti per rivestimenti dlc
Strati DLC (Diamond Like Carbon) innovativi per dare un maggior valore aggiunto al settore dei rivestimenti.
GASCON K2
Impianti innovativi di nitrurazione gassosa.
Gli impianti di nitrurazione gassosa GASCON racchiudono le migliori tecnologie per la nitrurazione gassosa. Sono costruiti modularmente per poter essere adattati alle specifiche esigenze di ogni Cliente ed offrono la possibilità di un controllo automatico del potenziale di nitrurazione.
Scopri nuovi orizzonti nel campo della nitrurazione gassosa con GASCON K2.
MICROPULS® Lotus
Cos'hanno in comune i fiori di loto e il nuovo sistema RUBIG PVD?
I fiori di loto hanno proprietà superficiali speciali che li proteggono dalle influenze esterne. Con la tecnologia PVD, vengono prodotte qualità superficiali protettive e migliorative simili.
Il sistema di rivestimento PVD MICROPULS® Lotus è stato sviluppato e realizzato per poter offrire ai nostri Clienti un pacchetto completo e innovativo.
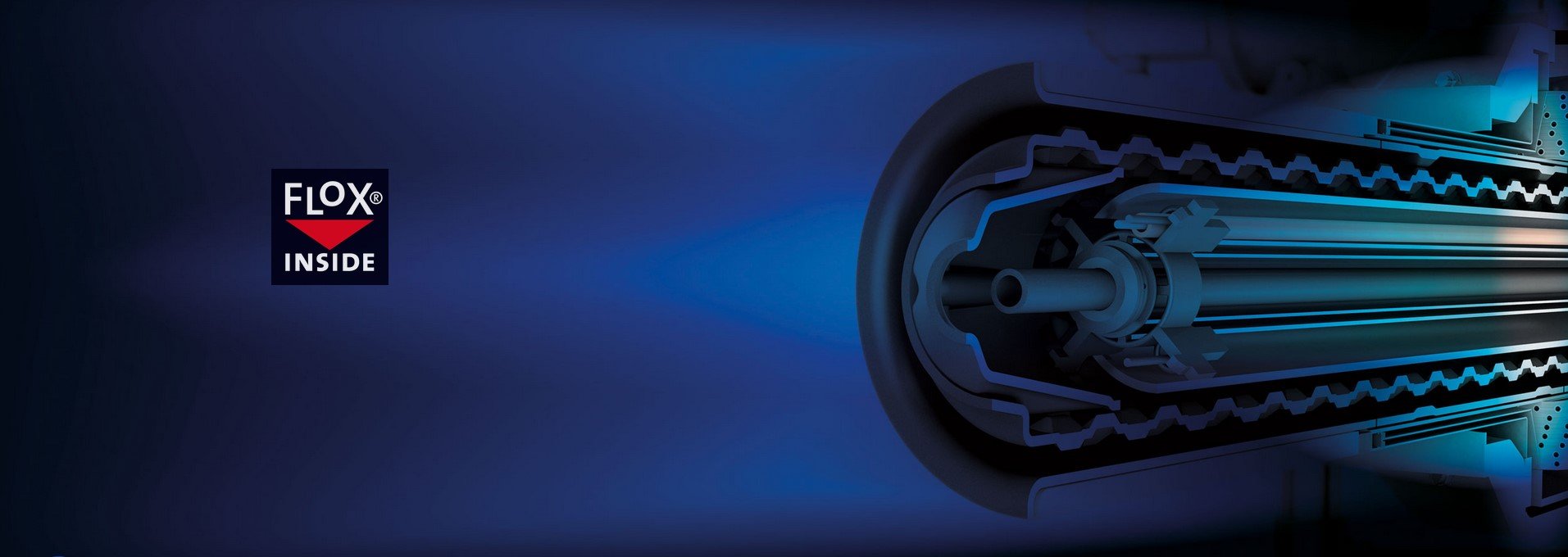
BRUCIATORI AD ALTO RENDIMENTO E BASSE EMISSIONI
WS Waermeprozesstechnik GmbH
Bruciatori recuperativi e rigenerativi ad alto rendimento e basse emissioni
La WS è specializzata nella progettazione e fabbricazione di bruciatori di gas ad altissimo rendimento e ridotte emissioni di NOx e tubi radianti per forni industriali. I bruciatori WS sono dotati di recuperatore di calore integrato al bruciatore con tecnologia FLOX® e vengono forniti già pre-assemblati e collaudati, pronti per il montaggio e per la messa in funzione.
Immagine: Rekumat CS 200, bruciatore con doppio recuperatore (a canali suddivisi e in SiC)
L'originale con oltre 30 anni di esperienza: fuoco senza fiamma!
L'enorme potenziale di FLOX® è stato subito evidente quando è stato scoperto l'effetto. La scomparsa della fiamma visibile e del tipico rumore ad essa associato, nonché la drastica riduzione delle emissioni di NOx durante la combustione.
“Fuoco senza fiamma”: sembra un paradosso e allo stesso tempo è una scoperta rivoluzionaria. Questo principio di combustione, che trova un'ampia gamma di applicazioni in numerose varianti, soprattutto nell'industria siderurgica e nei bruciatori per il trattamento termico, presenta vantaggi imbattibili. A differenza dei bruciatori convenzionali, la sofisticata miscelazione di gas combustibile, aria di combustione e gas di scarico di ricircolo nei bruciatori WS in funzionamento FLOX® evita picchi di temperatura di combustione. Pertanto, nonostante elevati tassi di preriscaldamento dell'aria comburente per aumentare significativamente l'efficienza, è possibile evitare il contemporaneo aumento delle emissioni di NOx. Inoltre, la distribuzione omogenea della temperatura nel forno garantisce prodotti di alta qualità e un'usura del bruciatore notevolmente ridotta. Tutti fattori importanti per un pensiero orientato all'ambiente, un'azione economicamente vantaggiosa e la produzione di prodotti di alta qualità.
REKUMAT®
I bruciatori auto-recuperativi della serie REKUMAT® è un best seller del quale sono stati venduti oltre 60.000 unità negli ultimi 30 anni. Durante tutti questi anni, sono stati sviluppati molti nuovi modelli con recuperatori in diversi materiali...
Schede tecniche
-
Bruciatori con recuperatore in SiC
-
Bruciatori con recuperatore ibrido in SiC ed a canali suddivisi
-
Bruciatori con recuperatore metallico
-
Bruciatori con recuperatore a canali suddivisi
REGEMAT®
Il principio rigenerativo per il pre-riscaldo dell'aria di combustione, oggi, per via degli elevati costi energetici, può essere applicato con successo anche a bruciatori di piccole taglie (fino a 400 kW) per il riscaldo di forni per nastri o di trattamento termico.
Schede tecniche
-
Bruciatore auto-rigenerativo per tubi radianti
-
Bruciatore auto-rigenerativo per riscaldo diretto
Video
Tubi radianti
Le performance di un sistema di combustione non dipendono solo dal bruciatore, ma, spesso, anche da un'appropriata scelta del tubo radiante più idoneo all'applicazione. I tubi radianti WS sono disponibili in diversi materiali e versioni.
Schede tecniche

SONDE A OSSIGENO E STRUMENTAZIONE PER IL CONTROLLO DEI TRATTAMENTI TERMICI
United Process Controls GmbH
Sonde a ossigeno, sonde a idrogeno, strumentazione e sistemi per il controllo e la regolazione dei processi termochimici
Da oltre 30 anni, la PROCESS ELECTRONIC, oggi UNITED PROCESS CONTROLS GERMANY, è specializzata nella progettazione di sonde a ossigeno, sonde a idrogeno, sistemi per il controllo, la regolazione e l'automazione dei processi termochimici di cementazione e nitrurazione gassosa.
Oltre a fornire sonde e programmatori per impianti di trattamento termico, offriamo soluzioni complete per il controllo di processo, per i sistemi per l'assicurazione della qualità e per l'ottimizzazione dei processi di produzione.
Siamo stati i primi a sviluppare e commercializzare il calcolo on-line per la diffusione del carbonio per garantire che il target di carbonio ed il profilo di durezza siano sempre rispettati.
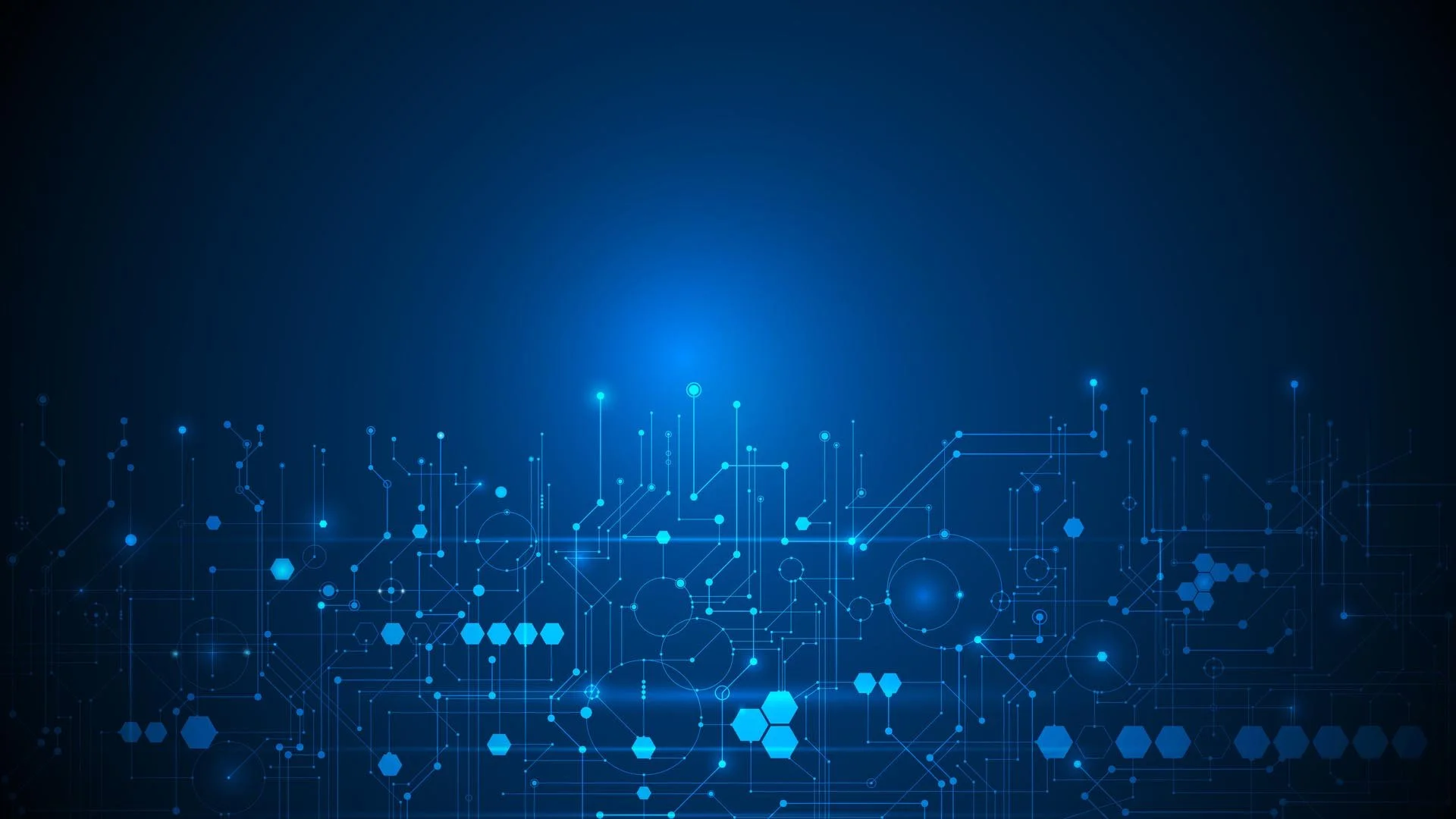
QMULUS
INTELLIGENZA ARTIFICIALE E MACHINE LEARNING PER I TRATTAMENTI TERMICI
United Process Controls GmbH
QMULUS è una piattaforma olistica che facilita e ottimizza il lavoro degli impianti trattamento termico, aumentando al contempo l’efficienza e consentendo un migliore processo decisionale.
In un mondo in cui le sfide economiche e ambientali incombono, l’industria del trattamento termico si trova a un bivio. È un regno in cui i processi necessitano di ottimizzazione, il consumo di energia richiede una riduzione e la qualità del prodotto insiste per raggiungere nuovi traguardi. In questo panorama dinamico, QMULUS, la piattaforma Industrial Internet of Things (IIoT) di UPC MARATHON, emerge come l'eroe della storia, brandendo un approccio olistico all'integrazione, alla normalizzazione e all'accessibilità dei dati. Intraprendiamo quindi un viaggio per comprendere le sfide affrontate dal settore del trattamento termico, il profondo impatto della trasformazione digitale e il modo in cui QMULUS è destinato a rimodellare la narrativa.
SFIDE: IL FRONTE DI BATTAGLIA DEL SETTORE
Pressione economica e ambientale
Immagina uno scenario in cui i prezzi del gas naturale continuano la loro incessante salita e le normative ambientali continuano a diventare più severe. Questo è il mondo in cui opera l'industria del trattamento termico. La richiesta di un'impronta di carbonio ridotta significa che ogni sottocomponente deve essere dotato di un certificato che ne garantisca la compatibilità ambientale. Tuttavia, per raggiungere questo obiettivo è necessario un completo rinnovamento digitale, il che significa che il settore deve passare a uno stato in cui prospera grazie a informazioni trasparenti e dettagliate. Questo spostamento verso la trasparenza e la digitalizzazione è vitale affinché l’industria rimanga competitiva e responsabile dal punto di vista ambientale.
Passare il testimone – Competenza nell’invecchiamento
Nel mondo del trattamento termico, gli esperti stanno diventando sempre più esperti e il trasferimento delle loro preziose conoscenze sta diventando sempre più impegnativo. Mentre questi esperti si preparano ad andare in pensione, portano con sé un patrimonio di competenze, spesso definito la “salsa segreta” del mestiere. La generazione più giovane è entusiasta e desiderosa di apprendere, ma la natura frenetica e attenta ai costi del settore non sempre consente un trasferimento graduale di tale conoscenza. Questa lotta ha un impatto di vasta portata sulle attrezzature, sui processi e, in ultima analisi, sulla qualità del prodotto.
Infrastruttura IT obsoleta
Immaginate questo: robuste apparecchiature per il trattamento termico che resistono alla prova del tempo, ma i sistemi responsabili del loro funzionamento sono bloccati in un'epoca passata. Silos di dati, software obsoleti e la mancanza di interfacce dati hanno creato collettivamente un caos digitale. In questo paesaggio caotico, le preziose informazioni accumulate nel corso degli anni giacciono dormienti, sepolte in tombe di dati inaccessibili. L’industria del trattamento termico si trova ora ad affrontare la pressante necessità di una pulizia digitale, una revisione attesa da tempo per sbloccare il potenziale non sfruttato nascosto nei suoi dati storici e modernizzare la sua infrastruttura digitale.
Requisiti rigorosi in materia di sicurezza IT e dati
In un mondo in cui Internet è ovunque, dietro ogni angolo virtuale si nascondono potenziali minacce informatiche che richiedono una vigilanza costante. La necessità di proteggere i dati sensibili è più cruciale che mai. Quadri normativi come il CMMC (Cybersecurity Maturity Model Certification) pongono le basi per rigorose misure di sicurezza informatica. L’industria del trattamento termico si trova non solo sulla strada della digitalizzazione, ma anche con il mandato di farlo in modo sicuro, garantendo che i dati personali, i segreti aziendali proprietari e le informazioni tecniche siano efficacemente protetti e rimangano sotto chiave digitale.
SOLUZIONE: LA TRASFORMAZIONE DEL SETTORE DEL TRATTAMENTO TERMICO, QMULUS PIONEERS
Nel competitivo settore del trattamento termico, QMULUS, la piattaforma IIoT all'avanguardia di UPC MARATHON, emerge come una forza trasformatrice. Offre una soluzione completa alle sfide del settore, trasformando efficacemente problemi come l’aumento dei costi energetici e le complessità normative in opportunità di eccellenza operativa. Più che un semplice strumento, QMULUS funge da alleato strategico, rimodellando le sfide in percorsi per il successo aziendale.
QMULUS eccelle nell'integrazione perfetta di diverse fonti di dati, nella definizione delle priorità delle metainformazioni e nell'implementazione dei processi di normalizzazione. Il risultato è un data warehouse completo che fornisce informazioni utili, migliorando la precisione del processo decisionale operativo. Affrontando le sfide poste dalle infrastrutture IT obsolete e dalla sicurezza dei dati, QMULUS garantisce il rafforzamento della vostra azienda contro le esigenze dell'era digitale.
QMULUS sviluppa il suo impatto trasformativo attraverso tre portali interconnessi: produttore, cliente e operatore. Questi portali non sono funzionalità autonome ma elementi strategici per orchestrare la trasformazione digitale della tua azienda. Il Portale del produttore fornisce approfondimenti in tempo reale per la manutenzione predittiva, il Portale del Cliente garantisce la tracciabilità trasparente delle informazioni sul prodotto e il Portale dell'Operatore consente il monitoraggio e l'analisi in tempo reale, ottimizzando ogni aspetto della tua attività. La spina dorsale intelligente di queste operazioni risiede nei sistemi di assistenza di QMULUS, che comprendono il rilevamento delle anomalie, i processi modello e gli strumenti di convalida.
QMULUS non è solo uno strumento; è una forza dinamica che plasma il futuro del settore del trattamento termico!
Articoli correlati:
CLICCA SULL’IMMAGINE A LATO ED UNISCITI A NOI PER UN WEBINAR RIVOLUZIONARIO SULL’INTELLIGENZA ARTIFICIALE NEL TRATTAMENTO TERMICO
Webinar
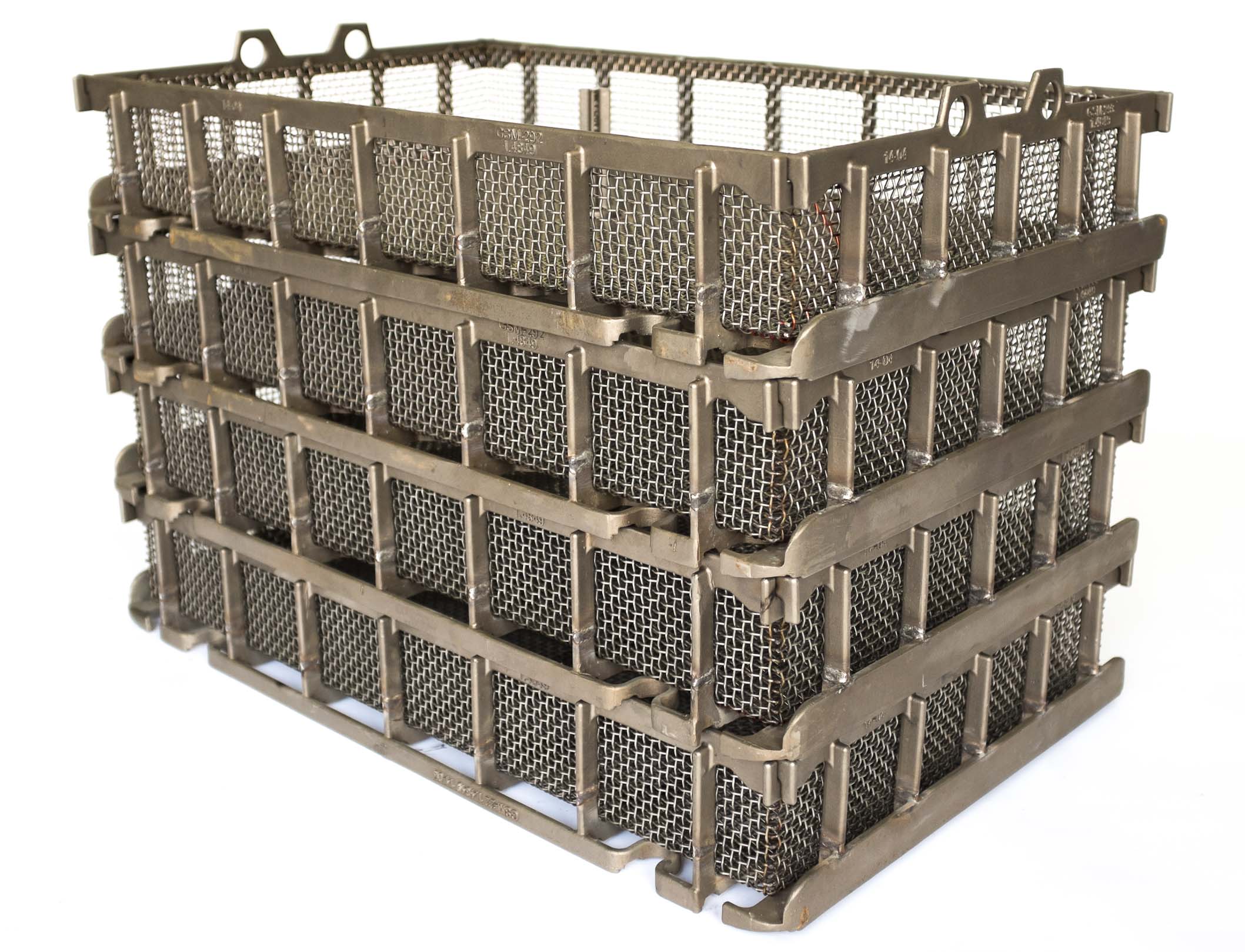
ATTREZZATURE PER TRATTAMENTI TERMICI E PER IL CARICAMENTO DEI FORNI
Attrezzature in leghe Ni-Cr per il caricamento di forni
Offriamo prodotti e soluzioni individuali per il trattamento termico. Approfittate della nostra esperienza e della nostra collaborazione con Partner industriali qualificati.
Il nostro servizio inizia da Voi. La gamma di applicazioni si estende dalle attrezzature di caricamento in fusione ai nastri trasportatori, dalle parti di ricambio alle costruzioni in saldato ed alle reti. Ciò ci rende il punto di contatto per tutti gli utilizzatori di forni per trattamenti termici.
Definiamo i requisiti. Ci occupiamo della realizzazione di disegni e di campioni per la produzione dei componenti richiesti. Dopo l'acquisto, continuerai a essere seguito dai nostri specialisti per tenere conto della tua esperienza e delle tue considerazioni in un'ottica di miglioramento continuo dei nostri prodotti e del nostro servizio.
Trai vantaggio dai nostri punti di forza:
Partner qualificati e certificati che dispongono dei macchinari più moderni e delle tecnologie più avanzate
Servizio e consulenza tecnica competente
Soluzioni individuali e personalizzate
Flessibilità e tempi di consegna rapidi
Oltre 50 anni di esperienza professionale
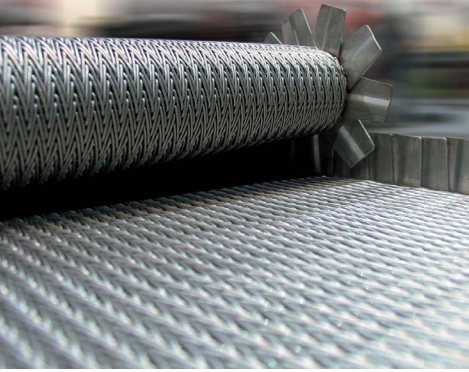
NASTRI METALLICI PER FORNI DI TRATTAMENTO TERMICO, SINTERIZZAZIONE E BRASATURA
CODINA S.A.
Nastri trasportatori metallici CODINA
I nastri trasportatori sono costituiti essenzialmente da fili congiunti che formano un nastro continuo, utilizzato per il trasporto dei pezzi nei forni. I nastri sono disponibili in molti materiali diversi per numerose applicazioni e processi con un'ampia gamma di temperature.
I nastri sono costruiti con spirali per tutta la larghezza e collegati con traversine dritte o incrociate. I bordi delle traversine sono saldati o collegati..
trattamenti termici
Il trattamento termico degli acciai è un processo che consiste in una serie di operazioni di riscaldamento e raffreddamento, in condizioni controllate di temperatura, velocità, tempo e pressione, di metallo o leghe allo stato solido, al fine di migliorare le loro proprietà meccaniche. Questo tipo di processo di produzione migliora notevolmente la durezza, la resistenza e l'elasticità dei materiali trattati.
I nastri utilizzati per questi processi sono realizzati principalmente nei seguenti materiali:
AISI 314 / 25-20 / 1.4841
Questo materiale è adatto per l'utilizzo in processi in cui la temperatura è compresa tra 900º e 1160 ºC. Tuttavia, questo materiale non è adatto a processi in cui il nastro lavora continuativamente tra 750 ° e 850 ° C, poiché diventa fragile per la formazione di fase sigma.
AISI 330 / 37-18 / 1.4864
Materiale per alte temperature che offre elevata resistenza meccanica e resistenza alla corrosione ed alla carburazione. Può funzionare a temperature fino a 1160 ° C. La proprietà principale di questo materiale austenitico è che rimane efficace nell'intervallo di temperatura della formazione di fase sigma (750-850ºC) e supporta la formazione di questa fase per un lungo periodo di tempo.
CODINA può produrre questi tipi di nastri con altri materiali su richiesta.
Alcune esecuzioni più comuni di nastri per trattamento termico:
A5 con sponde laterali
A1S
sinterizzazione
La sinterizzazione è un processo di produzione continuo in cui la temperatura della polvere metallica o ceramica è inferiore al punto di fusione della miscela di polvere pressata.
Questo processo è ampiamente utilizzato nell'industria automobilistica o in processi in cui il volume di produzione richiesto è molto elevato.
I nastri trasportatori svolgono una funzione chiave in questo processo per trasportare i pezzi all'interno dei forni ad alta temperatura che completano il processo di sinterizzazione. Pertanto, la selezione del modello e del materiale più idonei saranno molto importanti nella progettazione del nastro trasportatore.
I nastri utilizzati per questi processi sono realizzati principalmente nei seguenti materiali:
AISI 314 / 25-20 / 1.4841
Questo materiale è adatto per l'utilizzo in processi in cui la temperatura è compresa tra 900º e 1160 ºC. Tuttavia, questo materiale non è adatto a processi in cui il nastro lavora continuativamente tra 750 ° e 850 ° C, poiché diventa fragile per la formazione di fase sigma.
CODINA può produrre questi tipi di nastri con altri materiali su richiesta.
Alcune esecuzioni più comuni di nastri per sinterizzazione:
AE
AE-A
brasatura
La brasatura è un processo di fusione metallica per cui un metallo di riempimento viene riscaldato al di sopra del punto di fusione e distribuito tra due o più parti di fissaggio per azione capillare. Il metallo di riempimento viene portato leggermente al di sopra della sua temperatura di fusione (liquido) mentre è protetto da un'atmosfera idonea. Questo tipo di processo di produzione consente ai progettisti e agli ingegneri di produzione di unire geometrie semplici per ottenere componenti complessi.
Alcune applicazioni includono, tra gli altri: componenti aerospaziali, componenti automobilistici, dispositivi elettronici.
I nastri utilizzati per questi processi sono realizzati principalmente nei seguenti materiali:
AISI 314 / 25-20 / 1.4841
Questo materiale è adatto per l'utilizzo in processi in cui la temperatura è compresa tra 900º e 1160 ºC. Tuttavia, questo materiale non è adatto a processi in cui il nastro lavora continuativamente tra 750 ° e 850 ° C, poiché diventa fragile per la formazione di fase sigma.
AISI 330 / 37-18 / 1.4864
Materiale per alte temperature che offre elevata resistenza meccanica e resistenza alla corrosione ed alla carburazione. Può funzionare a temperature fino a 1160 ° C. La proprietà principale di questo materiale austenitico è che rimane efficace nell'intervallo di temperatura della formazione di fase sigma (750-850ºC) e supporta la formazione di questa fase per un lungo periodo di tempo.
CODINA può produrre questi tipi di nastri con altri materiali su richiesta.
Alcune esecuzioni più comuni di nastri per brasatura:
B1ES
B1DS

ATTREZZATURE IN FIBRA DI CARBONIO - CFC
KORNMEYER
Il Gruppo NIPON KORNMEYER CARBON
Le attrezzature in fibra di carbonio - CFC
La fibra di carbonio è un materiale avente una struttura filiforme, molto sottile, realizzato in carbonio, utilizzato in genere nella realizzazione di una grande varietà di "materiali compositi", così chiamati in quanto sono costituiti da due o più materiali, che in questo caso sono le fibre di carbonio e una cosiddetta matrice, in genere di resina (ma può essere in altro materiale plastico o in metallo) la cui funzione è quella di tenere in "posa" le fibre resistenti (affinché mantengano la corretta orientazione nell'assorbire gli sforzi), di proteggere le fibre ed inoltre di mantenere la forma del manufatto composito.
Per la realizzazione di strutture in composito le fibre di carbonio, vengono dapprima intrecciate in veri e propri panni in tessuto di carbonio e una volta messi in posa vengono immersi nella matrice. Il risultato finale è una struttura solida (che può avere la forma di una piastra, un tondo, un tubo, un foglio, ecc.) con eccellenti caratteristiche meccaniche, sia a freddo che a caldo
Tra le caratteristiche della fibra di carbonio spiccano l'elevata resistenza meccanica, la bassa densità, la capacità di isolamento termico, resistenza a variazioni di temperatura e all'effetto di agenti chimici, buone proprietà ignifughe.
Confronto tra attrezzature in lega Ni-CR e CFC .
Attrezzature in acciaio (leghe Ni-Cr)
Resistenza meccanica: diminuisce all’aumentare della temperatura
Massima temperatura di lavoro: 1150/1200 °C
Dilatazione termica: elevata (in funzione della lega)
Stabilità dimensionale: bassa
Peso specifico: ca. 8 kg/dm3
Resistenza agli shock termici: discreta (in funzione della lega, diminuisce con il
numero di cicli)
Resistenza agli urti meccanici: alta (in funzione della lega)
Resistenza alla fatica meccanica: buona (in funzione della lega, diminuisce con il numero di cicli)
Sensibilità agli agenti chimici: elevata
Attrezzature in CFC
Resistenza meccanica: aumenta all’aumentare della temperatura
Massima temperatura di lavoro: 2500 °C
Dilatazione termica: trascurabile
Stabilità dimensionale: elevata
Peso specifico: ca. 1,5÷2 kg/dm3
Resistenza agli shock termici: eccellente (in alcuni casi, possono essere superati i 18.000 cicli)
Resistenza agli urti meccanici: alta
Resistenza alla fatica meccanica: i sistemi CFC non sono suscettibili alla fatica
Sensibilità agli agenti chimici: inerte
I vantaggi delle attrezzature in CFC
Aumento della carica utile: un’attrezzatura in CFC pesa un 1/6 di una in acciaio.
Aumento del volume utile del forno: le attrezzature sono più sottili (circa la metà di quelle in acciaio) e, pertanto, lasciano più spazio ai pezzi da caricare.
Riduzione dell’inerzia termica: le attrezzature in CFC sono molto più leggere, quindi, a parità di pezzi trattati, si scaldano e si raffreddano più velocemente
Riduzione dei tempi di ciclo: poiché riscaldo e raffreddamento sono più rapidi, i cicli sono più brevi.
Risparmio energetico: per i motivi di cui sopra, l’energia necessaria è inferiore.
Migliore qualità del trattamento termico: minore massa da riscaldare e raffreddare migliorano l’uniformità del processo di tempra.
Migliore qualità dei pezzi trattati: la perfetta planarità e la stabilità nel tempo riducono le deformazioni dei pezzi.
Facilità di caricamento: la stabilità dell’attrezzatura facilita il caricamento dei pezzi e consente il caricamento robotizzato.
Riduzione dei tempi di caricamento: il peso ridotto delle attrezzature in CFC ne facilita la movimentazione.
Riduzione dello spazio di stoccaggio: la leggerezza delle attrezzature in CFC riduce lo spazio necessario per lo stoccaggio delle stesse anche su strutture di sostegno più semplici.
Riduzione dei costi di manutenzione: le attrezzature in CFC non richiedono alcuna manutenzione.
Applicazioni
- Cementazione in bassa pressione
- Sinterizzazione-
- PVD/CVD
- Brasatura in vuoto
- Atmosfere inerti e trattamenti in vuoto
Il nostro team di tecnici progetta la soluzione più adeguata per il processo di trattamento termico mediante l'utilizzo di programmi CAD e simulazioni di calcolo del carico all'avanguardia.
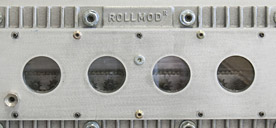
SISTEMI A TENUTA DI GAS PROTETTIVO PER FORNI A RULLINI
ROLLMOD GmbH
Il sistema di trasporto brevettato ROLLMOD
I sistemi di trasporto a rulli vengono utilizzati sulle linee di produzione per ottenere un riscaldamento uniforme dei componenti prodotti senza alcuna perdita di calore. I sistemi di trasporto con avanzamento a strato singolo e diametri di rulli piccoli sono i più indicati per tali usi. La sfida tecnologica a questo proposito è quella di risolvere problemi di progettazione e funzionamento relativi agli azionamenti, allo stoccaggio dei pezzi ed alla tenuta del gas protettivo. I sistemi brevettati ROLLMOD combinano questi elementi in moduli intercambiabili, di facile manutenzione, precisa ed economica.
Sistema di trasporto tradizionale:
- rulli metallici D > 100 mm
- rapporto T/D > 2
Sistema a rullini ROLLMOD:
- rulli ceramici D < 60 mm
- rapporto T/D < 2
Il sistema a rullini ROLLMOD non richiede più l'utilizzo di pesanti attrezzature di caricamento, perché i pezzi da trattare sono posizionati direttamente sui rullini oppure su vassoi leggeri.
I forni possono essere riscaldati da tubi radianti (con resistenze elettriche o bruciatori recuperativi) posti sopra e sotto i rulli. Le prestazioni e le temperature massime sono adattate alle specifiche del Cliente. Le unità del modulo ROLLMOD possono essere collegate a tutti i moderni sistemi di controllo utilizzati nelle linee di produzione. I comandi gestiscono le operazioni con gas inerte o gas reattivi (ad es. con potenziale di carbonio controllato mediante sonda a ossigeno) e regolano la temperatura e la velocità.
La produzione può essere impostata e adattata a cicli fissi con quasi qualsiasi velocità. Ciò vale anche per i trasportatori a velocità controllata con sensore fotoelettrico (opzionali) posti all'entrate ed all'uscite del forno.
Modulo con minimo spazio tra i rulli per il trasporto di piccoli componenti da 40 mm di diametro senza vassoi. Manutenzione semplice grazie al design modulare per l'azionamento, l'immagazzinamento, l'isolamento e la tenuta del gas.
Modulo con design modulare a basso costo, utilizza azionamenti singoli a bassa manutenzione con rulli fino a 60 mm di diametro e larghezze fino a 3.000 mm.
FORNI PER I TRATTAMENTI TERMICI E PER IL RISCALDO
THERMCONCEPT GmbH
L’esperienza al vostro servizio
Thermconcept nasce a Bremen (Germania), “La città dello spazio”, così chiamata per via delle numerose aziende ed istituti scientifici che lavorano nel settore aerospaziale, automobilistico, della mobilità elettrica e dell’energia eolica. Grazie a questo background ha potuto sviluppare prodotti di alta tecnologia ed ottenere conoscenze avanzate, offrendo al cliente finale prodotti di alta qualità.
Con la propria pluridecennale esperienza Thermconcept produce forni a camera, a carro, a nastro, per bagni di sale, riscaldati sia elettricamente che a gas, per temperature di lavoro da 50 °C a 2000 °C.
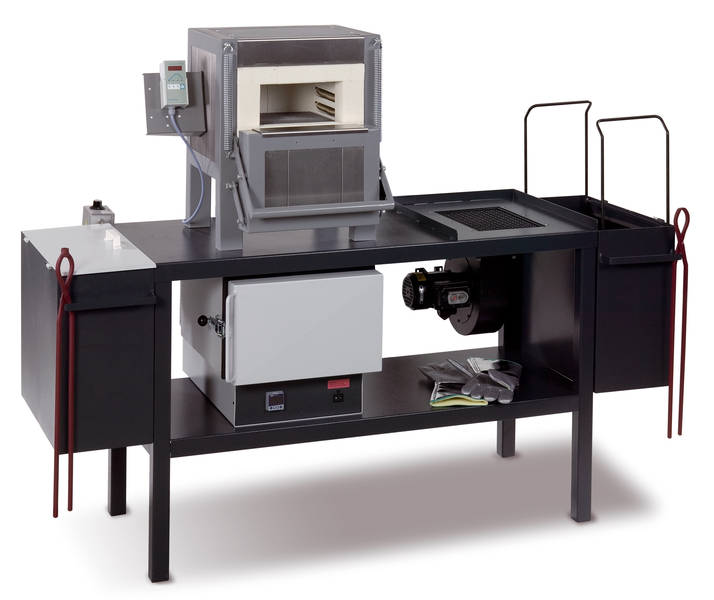
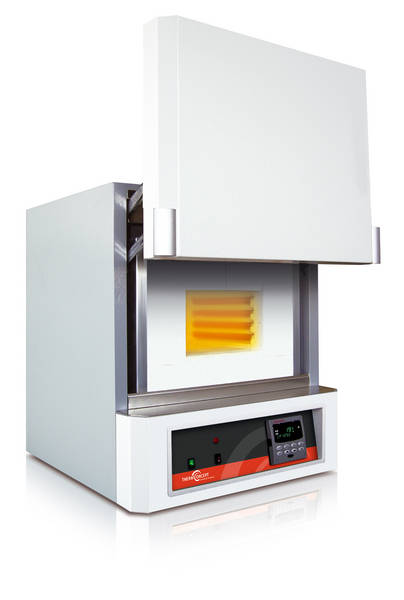
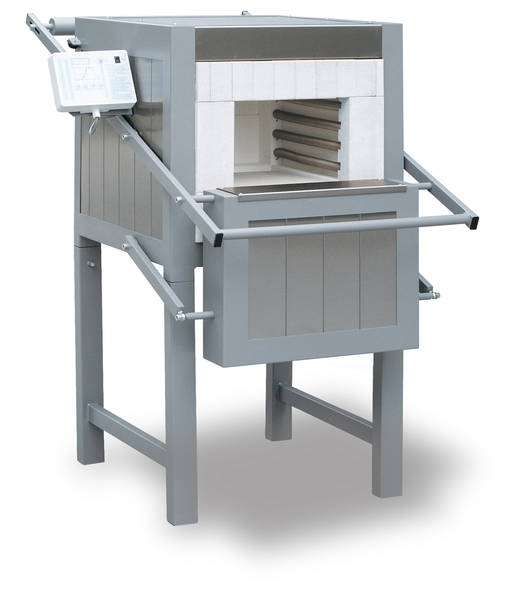
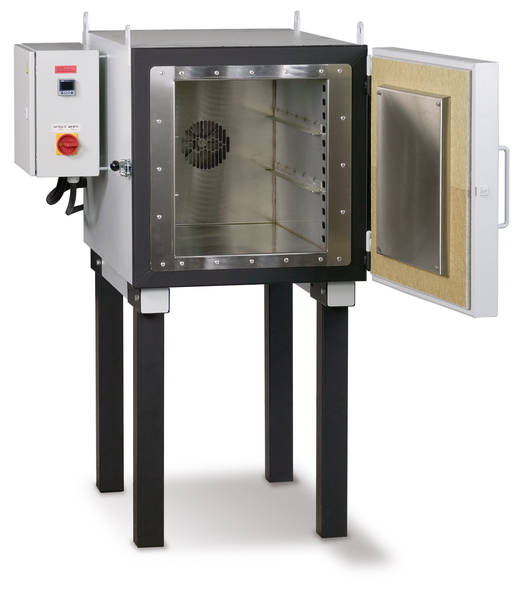
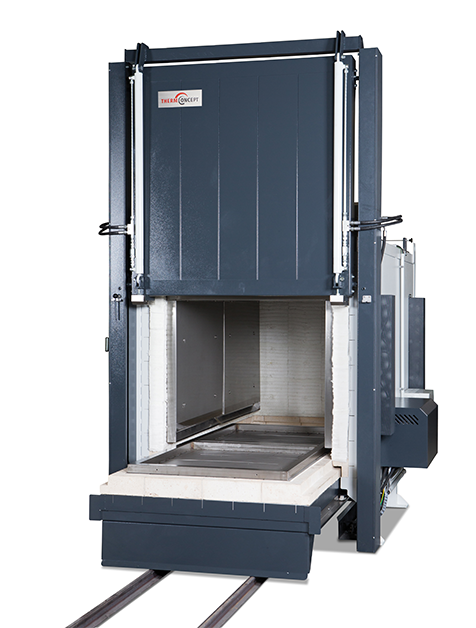
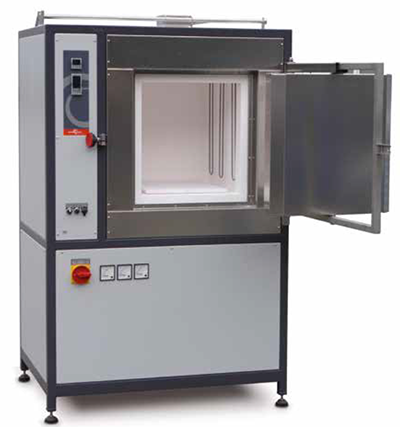
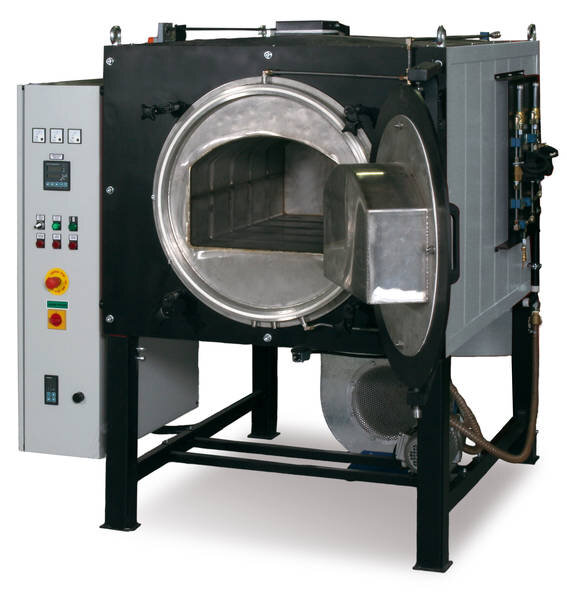

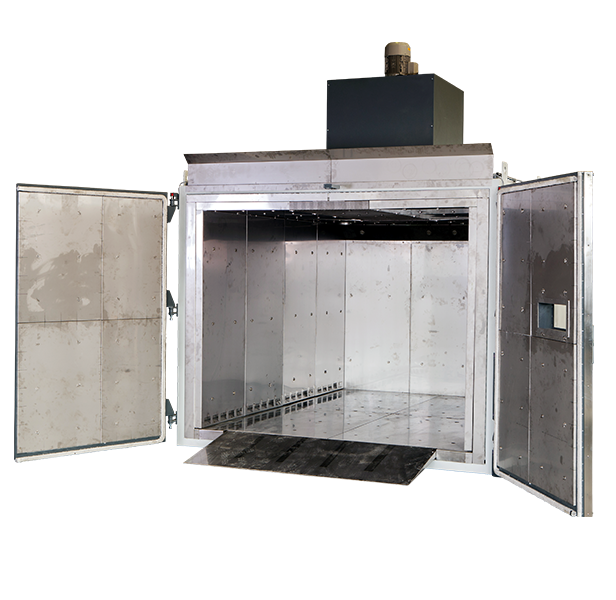
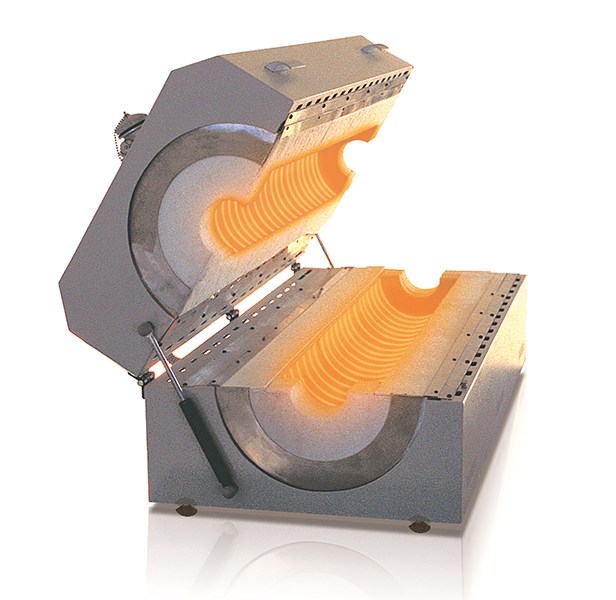
Un forno per ogni vostra esigenza
Oltre alla nostra gamma standard di forni, possiamo offrire sistemi personalizzati per esigenze specifiche del Cliente., anche per applicazioni di ricerca e laboratorio, per il trattamento di metalli non ferrosi, rinvenimento, tempra, laboratorio dentale, ceramica e vetro. Scarica il nostro catalogo in inglese dei prodotti relativo al tuo settore.
Scarica il Catalogo completo
Scarica il Catalogo completo
Scarica il Catalogo completo
Scarica il Catalogo completo
Scarica il Catalogo completo
Scarica il Catalogo completo

VERNICI PROTETTIVE
E PRODOTTI AUSILIARI
Vernici protettive, prodotti chimici
e di consumo
Sali e granulati, paste e vernici per la protezione da tempra, ossidazione, cementazione e nitrurazione; fogli inox per la protezione dei pezzi e lamierino d'acciaio per il controllo del potenziale di carbonio; cassette per tempra con granulati inerti. Accessori e dispositivi di protezione.

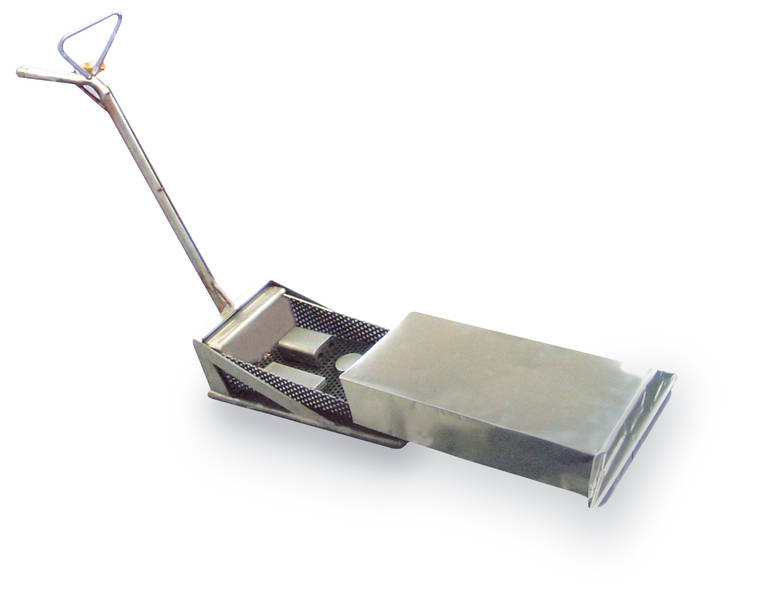
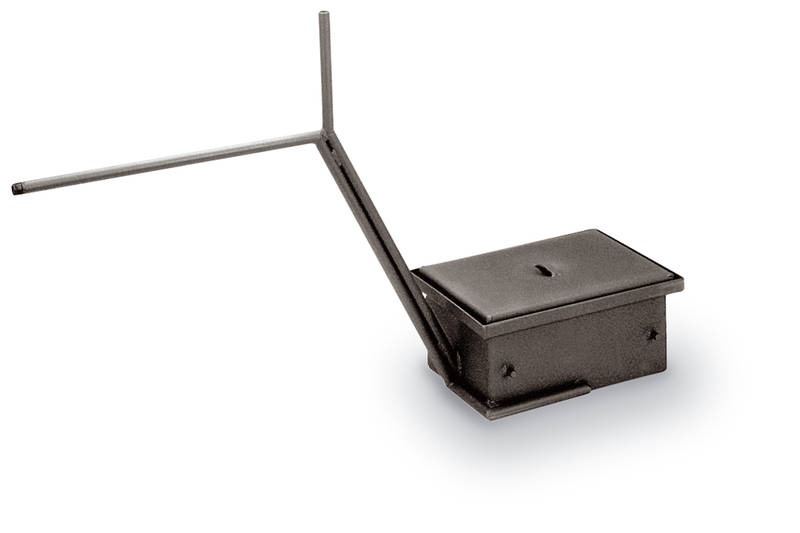
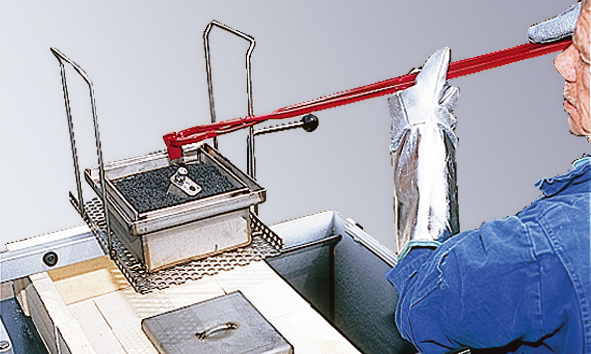
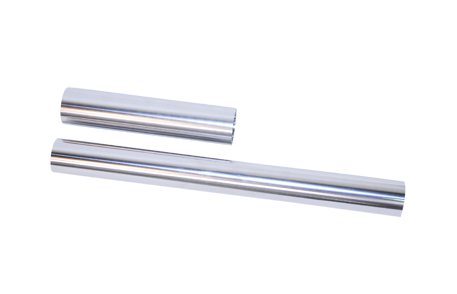
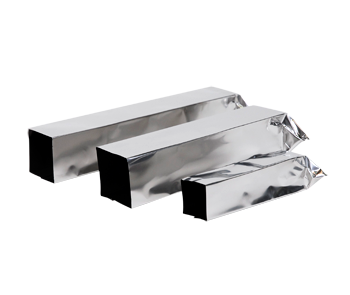
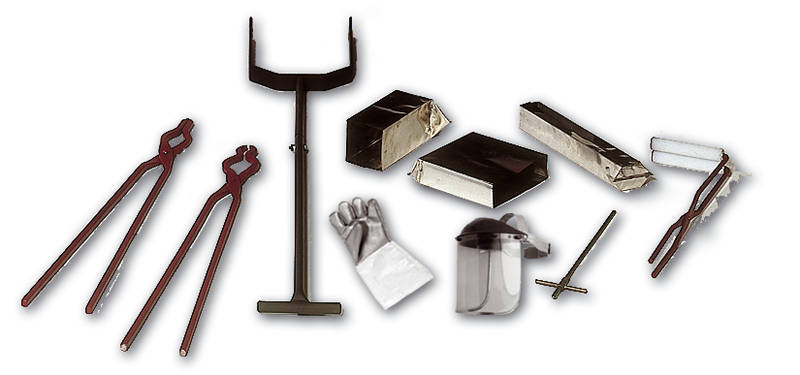
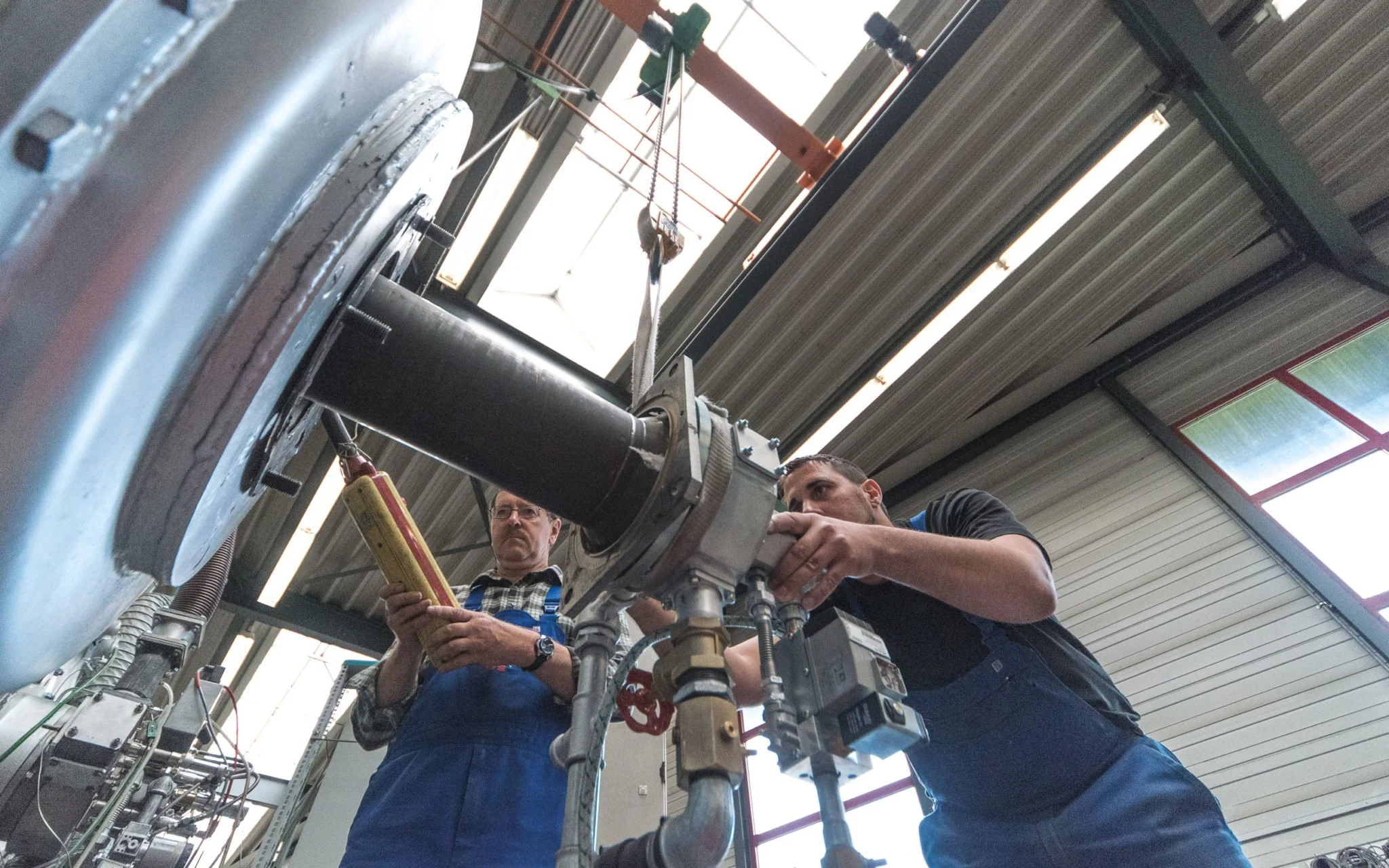
SERVIZIO ASSISTENZA TECNICA
Riparazione sonde a ossigeno, manutenzione bruciatori ed analisi della combustione
Il nostro servizio di assistenza tecnica:
professionalità e puntualità!
Le moderne tecnologie di processo offrono prestazioni eccellenti e richiedono una conoscenza adeguata: l'assistenza tecnica su prodotti tanto evoluti è un mix equilibrato di esperienza e professionalità. La nostra ricetta è semplice: formazione costante del personale, apparecchiature di ultima generazione e logistica agile ed efficiente. Il risultato? Un supporto tecnico unico nel settore, per qualità e velocità di intervento. Un servizio d'eccellenza dedicato a tutti i clienti UPC-Marathon e WS.
La ATTAS in collaborazione con le proprie Rappresentate, offre i seguenti servizi:
assistenza e manutenzione bruciatori e impianti di combustione di forni industriali, analisi della combustione
servizio riparazione sonde a ossigeno per forni di trattamento termico
Analisi della combustione
La verifica periodica dell’impianto di combustione garantisce qualità costante dei cicli di trattamento termico, risparmio energetico e riduzione dell’emissioni nell’ambiente.
Grazie alla nitrurazione al plasma e a gas, gli stampi per forgiatura ottengono maggiore resistenza all’usura e durata operativa. RUBIG, forte di 80 anni di esperienza, offre soluzioni ideali per ambienti ad alta sollecitazione meccanica. Le tecnologie avanzate PVD permettono trattamenti precisi e sostenibili, riducendo tempi di fermo e costi per pezzo. Il processo è adatto anche per materiali complessi come 1.2343 e 1.2344. La nitrurazione multistrato garantisce prestazioni elevate e risultati ripetibili.